When choosing a fire retardant for their formulation, polymer manufacturers must weigh many factors besides effective reduction of flame and smoke. Companies must balance the demands of stakeholders inside and outside their organizations while considering practical, regulatory, and technical requirements. They must choose a fire retardant that:
- Is non-halogenated to alleviate concerns about possible toxicity
- Doesn’t significantly reduce the physical and mechanical properties of the polymer product
- Has a limited impact on the formulation cost
But one of the most critical properties of a fire retardant is
thermal stability. A fire retardant must be able to stand up to polymer melting temperatures in the manufacturing process. That requirement can be a limitation for many fire retardants.
Many manufacturers look for a fire retardant that can be applied across a range of processes and temperatures. While some fire retardants such as ATH (alumina trihydrate) are not stable above 200°C (392°F),
20 Mule Team® Borax
Firebrake® 500
is thermally stable up to 600°C (1112°F), making it suitable for processing in any polymers.
High-temperature polymer processes
Heat is key to the
polymer manufacturing process. To ensure the polymer formulation ingredients are well mixed and the product is consistent throughout, the polymer must be melted. Thus, any fire retardant added to the heated polymer must be able to withstand the processing temperature. Melt temperature depends on the polymer type, so the fire retardant you choose may have to withstand a range of potential high temperatures.
Many fire retardants can release water into the formulation when heated. Even very low amounts of water can affect the processability of almost all plastics. Polymers such as Nylon 6, Nylon 6/6, PET (polyethylene terephthalate), and PBT (polybutylene terephthalate) are particularly moisture sensitive in their molten state.
Water creates a variety of product defects by acting in the process in two ways:
- Moisture can create cosmetic issues, resulting in unacceptable product quality. In melted polymer, moisture will boil when pressure is relieved at the die lips, creating bubbles, pits, or dotted lines on the product surface. Added water above just 0.1% can make visible marks in extrusion.
- Water also reacts chemically with some polymers and degrades their properties. This hydrolysis reaction breaks the bonds in the polymer chains, which can result in significant reduction of the product’s mechanical properties.
Anhydrous zinc borate: Firebrake 500
Firebrake 500 (2ZnO 3B
2O
3) is an anhydrous zinc borate, which means it contains
no water. The product is made by dehydrating
Firebrake ZB at high temperatures. After the product is dehydrated, it is milled to meet the wet screen specification of less than 0.01% retained on U.S. mesh 100 screen and less than 0.10% retained on U.S. mesh 325 screen. The final product is packaged in 2,000 lb IBC bags or 25 kg bags.
Firebrake 500 is a multifunctional fire retardant and is used in a variety of polymers. Since it contains no water of hydration, it is stable up to 600°C and can be used in polymer systems requiring very high processing temperatures. Manufacturers can add it by using extruders, calenders, or injection molding equipment in the same way as other solid polymer additives.
Firebrake’s proven properties make
Firebrake 500 a preferred flame retardant for a variety of polymers including polyamide, polyetherketone, polysulfone, fluoropolymer, and polyester.
TGA curve of Firebrake ZB and Firebrake 500. Firebrake 500 shows no weight loss when heated up to 700°C (1292°F).
Firebrake 500 should be stored in a sealed container until use as the particle surface can gradually absorb moisture in high humidity environments.
Firebrake 500 for polymers: Additional benefits, faster action
Studies have shown numerous benefits of using
Firebrake 500. As a fire retardant, it has been found to be an effective smoke suppressant in chlorofluoropolymers and can completely replace antimony oxide in high-temperature polyamide applications.
Like
Firebrake ZB, it can improve comparative tracking index (CTI), thermal stability, and color stability of polyamide containing halogen sources. It is also reported to be effective in reducing heat release rate HRR (HRR) of polyetherketones and polysulfones.
Firebrake 500 in silicone-polyimide is shown to prevent dripping and meets the surface flammability and flame-ignition test requirement.
In addition, although this anhydrous zinc borate is recommended for use in polymers that are processed at 290°C or higher, there are potential benefits of using this fire retardant in lower processing temperature polymers such as those required for processing polyolefins and silicones.
- In an EVA/MDH/silica system, Firebrake 500 shows a lower HRR than Firebrake ZB
- It is believed that Firebrake 500 can promote sintering (ceramic formation) more readily than Firebrake ZB because it does not need to undergo endothermic dehydration before the promotion of sintering
- In addition, the fact that dehydration wouldn’t occur when the polymer is subjected to a fire also provides dimensional stability benefits in some applications
- Firebrake 500 has also shown faster action in silicone rubbers
A partner you can trust for fire retardant for polymers
For polymer manufacturers, ensuring a balanced and effective formulation is critical. The experts at U.S. Borax are leaders in research and innovation for borates who also have deep experience with polymer manufacturing. Our technical support team is here when you need assistance with any step, from selecting the right fire retardant for your process to perfecting your formulation.
With our rich technical expertise, exceptional customer service, and global shipping networks, you can count on U.S. Borax to be there when your company needs us.
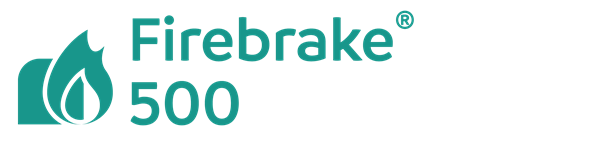
Resources