In borate mining’s early days, it took 10 days for the iconic 20 mule teams to carry borax ore across the Mojave Desert and reach a refinery for processing.
Now? The process from mine to market is considerably faster, thanks to the innovations of our transportation and logistics teams.
From mules to railroads to trucks using renewable diesel fuel, we’re proud of how we’ve overcome borate mining transportation challenges, anticipated technology progression, and shaped logistics over the course of 150 years.
With the pioneering spirit of our people, we helped transform an industry where transportation was time-intensive and extremely manual into a sophisticated, streamlined logistics network.
Rudimentary beginnings
The first borate mines were situated in remote, rugged locations. Such isolation made transportation a nightmare.
Early miners had to determine how to move equipment across long distances to develop a new mine. Once built, then came the most important challenge: How to get borax ore to market.
In 1883, we started using teams of 20 mules to carry 20 tons of ore 165 miles to a rail spur. These teams battled draining heat with scarce supplies, showcasing the fortitude that eventually led to the creation of the iconic 20 Mule Team® brand.
The railroad era
With production accelerating, our founder Francis M. Smith relentlessly pursued a better, faster way to deliver borax to market. The answer? Railroads.
Smith introduced a steam engine he named “Old Dinah,” a less taxing form of transportation, in the hopes of replacing the mules. However, steep grades proved too much for the engine, as she broke down frequently.
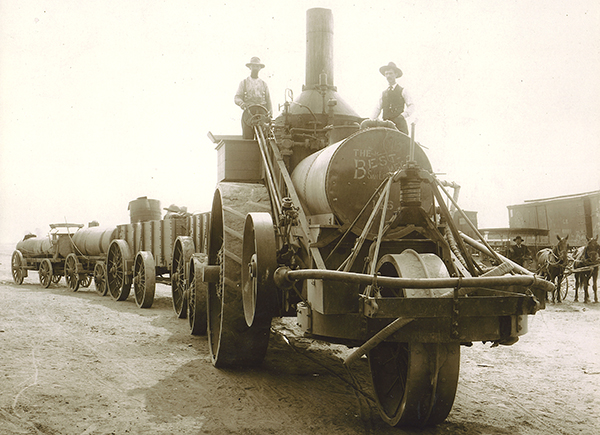
The steam engine pulling the ore wagons and water tanks.
After retiring the engine, Smith continued his dream of railroad development by submitting a request to the California State Railroad Commission, asking for money to develop a new line to connect mining sites to the Tonopah & Tidewater Railroad. The commission denied the request, spurring Smith to form his own railroad company: The Death Valley Railroad (DVRR).
Through the 1910s, the DVRR developed connections from mines to the T&T Railroad. One noteworthy extension was called “Baby Gauge Railroad” because it was only two feet wide, instead of the standard 36-inch gauge. Its narrower gauge enabled it to better navigate the steep surrounding mountain landscape.
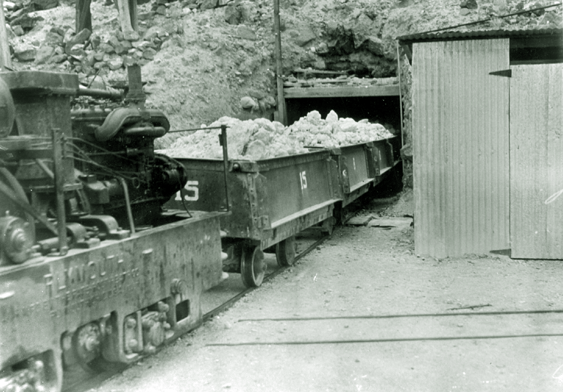
Ore coming from the Widow Mine on the Baby Gauge rail.
This period of mergers and expansions made borate mining transportation faster and easier.
Shaping the modern era
Borate demand continued to rise throughout the 20th century, requiring crafty innovations in transportation and logistics to match. Among these innovations, three key developments stand out.
Wilmington Port
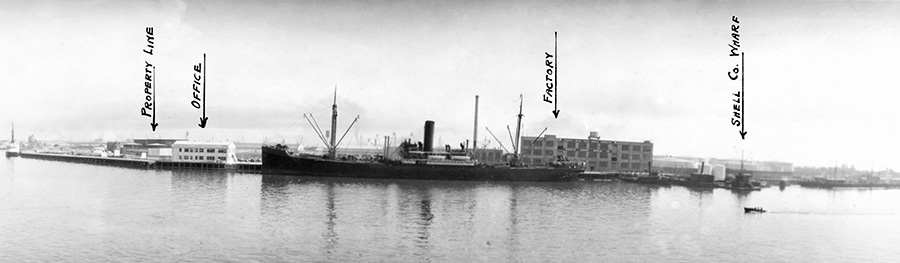
When we acquired the port location for our Wilmington refinery, the move was seen as visionary. Traditionally, rail cars took borates from the West Coast to East Coast refineries, then the material was loaded onto ships to travel across the Atlantic to Europe.
The opening of the Panama Canal in 1914 made Wilmington more cost-effective, creating a vastly shorter route to move borax east.
Wilmington itself was a state-of-the-art facility; the deep port became the first reinforced concrete industrial structure in Southern California.
Still going strong today, Wilmington remains the only privately owned property in the Port of Los Angeles.
Underground to open-pit mining
The largest project in U.S. Borax history unlocked exciting opportunities to leverage new transportation equipment.
Converting the underground mine at Boron to an open pit created more space, which led to the adoption of trucks to haul ore to the surface and around the mine.
Ever since the 1960s, when the first 100-ton haul trucks were used, we’ve continued to get bigger and more efficient equipment. Now, our fleet features giant haul trucks with 260-ton carrying capacity.
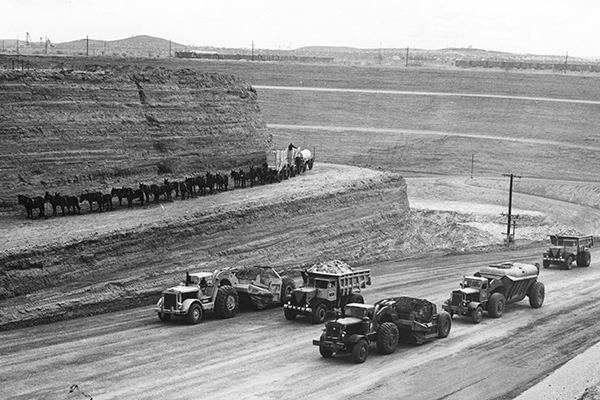
The 20 Mule Team and their 1960s counterparts in the open pit mine at Boron.
Recently, we embarked on an exciting trial to make U.S. Borax operations more environmentally friendly and sustainable. In December 2021, our first renewable diesel-powered truck came online.
In addition as part of, Rio Tinto we are excited about the one-year biofuel partnership pilot with bp, an important project with the potential to significantly decarbonize operations.
Storage and shipping enhancements
In spring 1952, we began construction on a new bulk shipping terminal at Wilmington, which featured loading facilities and 12 120-foot siloes.
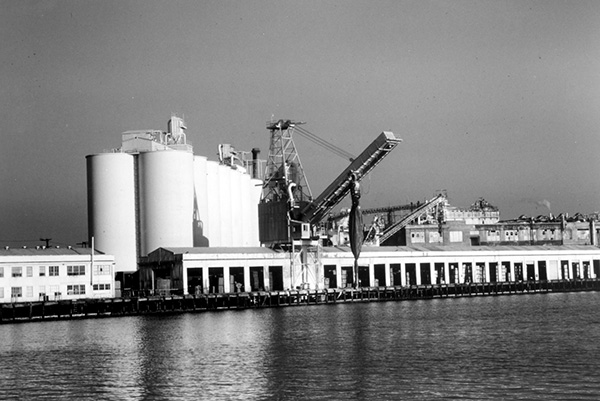
Wilmington in the 1960s
The update made it easier to load both raw and refined borates for ocean shipments to our Rotterdam warehouse, improving our competitive standing in Europe.
Nearly a decade later, we made a similar update at Boron operations where we built 12 100-foot storage siloes.
Logistics: Now and in the future
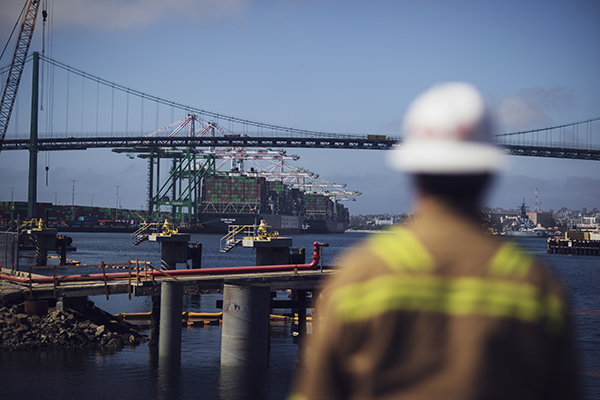
We’re still improving transportation and logistics in borate mining to meet the needs of today’s consumers and enable future progress.
As the trusted refined borates supplier for about 30% of global demand, we’re constantly investing in safer and more environmentally friendly equipment.
Interested in learning more about our history over the last 150 years? Visit the history page. Or plan a trip to our Borax Visitor Center and experience the rich history of mining innovation.
Resources