After World War II, consumer demand returned with renewed zeal. This rapid spike extended to borate-based products, from borosilicate heat-resistant glass products to agricultural fertilizers to ceramics and soaps.
Such high borate demand presented an exciting challenge for U.S. Borax: We needed to produce more, faster.
Unlike the early days of borate mining, it wouldn’t be a matter of searching for new borate ore deposits. Rather, this dilemma required special engineering ingenuity to modernize operations at our Boron site.
Fueled by significant advances in machinery and better geophysical knowledge of the borate deposits at Boron, company leadership made the pivotal decision to convert the underground mine into a surface mine.
This conversion was the largest undertaking in U.S. Borax history, led by two incredible men, engineer Bob Kendall and PhD chemist Howard Steinberg. Even before we finalized plans, it became clear this project would change the course of borate mining operations forever.
The conversion process
One particular characteristic made the Boron site an exceptional choice for open-pit mining operations. Borate ore sat close to the surface, at a depth of only a few hundred feet.
By converting the mine to an open-pit model, we could significantly reduce mining costs and recover higher amounts of ore. In traditional underground mining, infrastructure such as roofs and walls must be supported, which limits the amount of material available for extraction.
Open-pit mining also made it easier to:
- Transport ore with heavy machinery
- Maneuver around the mine
- See potential safety issues and prevent emergency situations
While the benefits were clear, plenty of variables could cause trouble. A project of this magnitude required precise engineering, and a large amount of capital to make it a reality.
From an engineering perspective, designing the open pit mine to enable growth, yet meet stringent safety demands, proved challenging. Important considerations were:
- Determining the slope of pit walls
- Positioning haul roads
- Handling mine tailings
The initial excavation resulted in a 275-foot-deep by 2,000-foot long by 1,700-foot-wide pit. It took an army of machines to displace 10 million tons of dirt. Once we finalized plans in early 1954, the conversion process took almost four years to complete; operations officially came online in late 1957.
More than a mine makeover
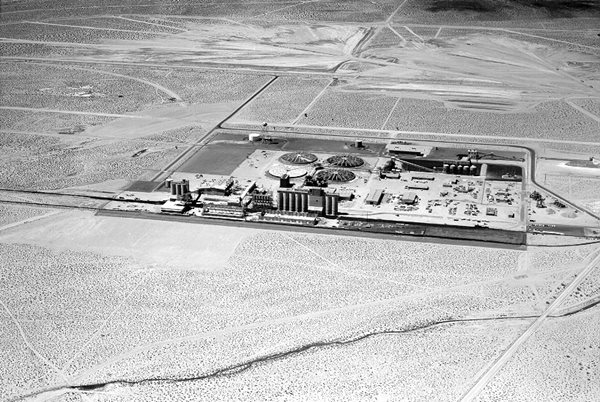
The new refinery at Boron operations in 1957.
Modernization efforts at our Boron site didn’t stop at the pit. We built and installed new equipment to improve production efficiency, including:
- Continuous mechanical miners
- 100-ton haul trucks
- Mechanical belt
- A new processing plant
Continuous mechanical miners
Unlike previous drilling and blasting methods, these new machines cut ore at the face of the mine, making extraction a substantially safer and more efficient process.
Haul trucks
With more space came a new fleet of 12 haul trucks featuring 100 tons of capacity. The trucks simplified the logistics of moving larger amounts of borates.
Mechanical belt
Three years after the conversion, we installed the world’s largest ore belt conveyor system to transport ore to the surface. The belt revolutionized the process, an early example of automation in borate mining.
Processing plant
An on-site processing plant accelerated operations as it eliminated the need to send material to Wilmington, the site of our first refinery. When building the plant, our engineers accounted for the different grades of ore that could be recovered with open-pit mining.
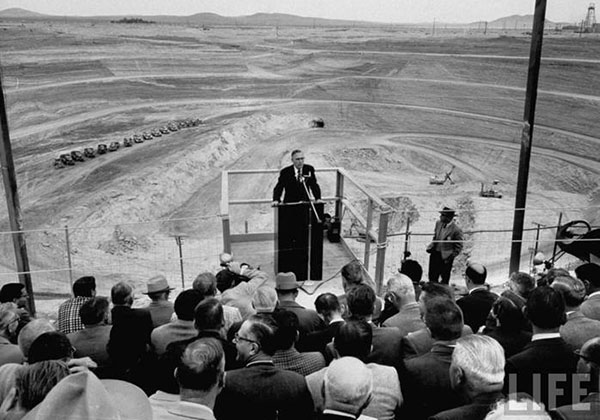
The dedication of the open pit mine with the new haul trucks in the background.
Building on the open-pit legacy
Since the conversion, we’ve continued to enhance efficiency, improve safety, and minimize our environmental impact.
Today, we supply about 30% of the world’s refined borates. Our high-quality products are essential to the modern products people use every day.
Throughout our 150 years in borax mining, our people have proved their pioneering spirit is what leads to true innovation. The engineering genius behind the open pit mining conversion is one especially great example of the legacy of innovation.
Resources